State-of-the-art technology in plastic extrusion for modern industries
State-of-the-art technology in plastic extrusion for modern industries
Blog Article
A Comprehensive Overview to the Process and Advantages of Plastic Extrusion
In the large realm of production, plastic extrusion arises as a very reliable and essential process. Translating raw plastic into continual profiles, it provides to a myriad of markets with its impressive versatility.
Recognizing the Fundamentals of Plastic Extrusion
While it might show up complicated at very first look, the procedure of plastic extrusion is fundamentally easy. The procedure starts with the feeding of plastic product, in the kind of powders, pellets, or granules, right into a warmed barrel. The designed plastic is then cooled, solidified, and reduced into desired lengths, finishing the process.
The Technical Refine of Plastic Extrusion Explained
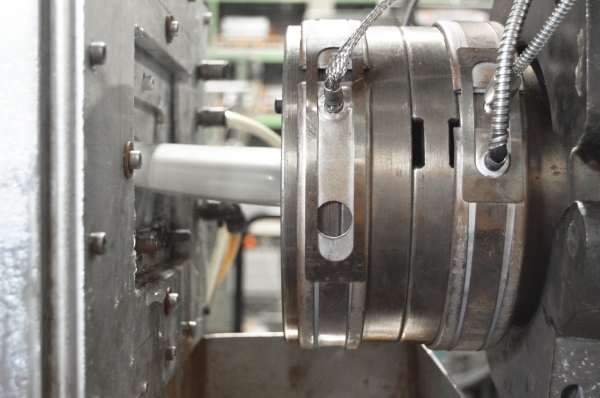
Kinds Of Plastic Suitable for Extrusion
The choice of the ideal type of plastic is a critical aspect of the extrusion process. Various plastics provide unique properties, making them more matched to certain applications. Polyethylene, for instance, is commonly utilized as a result of its affordable and very easy formability. It uses superb resistance to chemicals and dampness, making it ideal for items like tubes and containers. In a similar way, polypropylene is another popular option as a result of its high melting point and resistance to exhaustion. For more durable applications, polystyrene and PVC (polyvinyl chloride) are commonly selected for their toughness and resilience. Although these prevail choices, the choice eventually relies on the specific demands of the product being produced. Understanding these plastic kinds can dramatically enhance the extrusion procedure.
Comparing Plastic Extrusion to Other Plastic Forming Approaches
Understanding the kinds of plastic suitable for extrusion paves the means for a wider discussion on how plastic extrusion stacks up against various other plastic developing techniques. Plastic extrusion is unrivaled when it comes to producing continuous profiles, such as gaskets, pipes, and seals. It additionally permits for a constant cross-section along the size of the product.
Trick Advantages of Plastic Extrusion in Production
In the world of manufacturing, plastic extrusion supplies many substantial advantages. One noteworthy advantage is the cost-effectiveness of the procedure, that makes it a financially enticing manufacturing method. Furthermore, this technique offers superior product flexibility and boosted manufacturing speed, thus boosting total manufacturing efficiency.
Affordable Production Approach
Plastic extrusion leaps to the center as an affordable production technique in production. This procedure stands apart for its capacity to generate high volumes of product promptly and efficiently, providing suppliers with significant cost savings. The primary cost advantage is the ability to utilize less costly raw products. Extrusion uses polycarbonate materials, which are less expensive compared to ceramics or steels. Additionally, the extrusion procedure itself is fairly straightforward, lowering labor costs. Furthermore, plastic extrusion needs less power than typical production approaches, adding to lower operational costs. The procedure also reduces waste, as any kind of excess or defective materials can be recycled and recycled, offering one more layer of cost-effectiveness. Generally, the economic benefits make plastic extrusion a very attractive choice in the production industry.
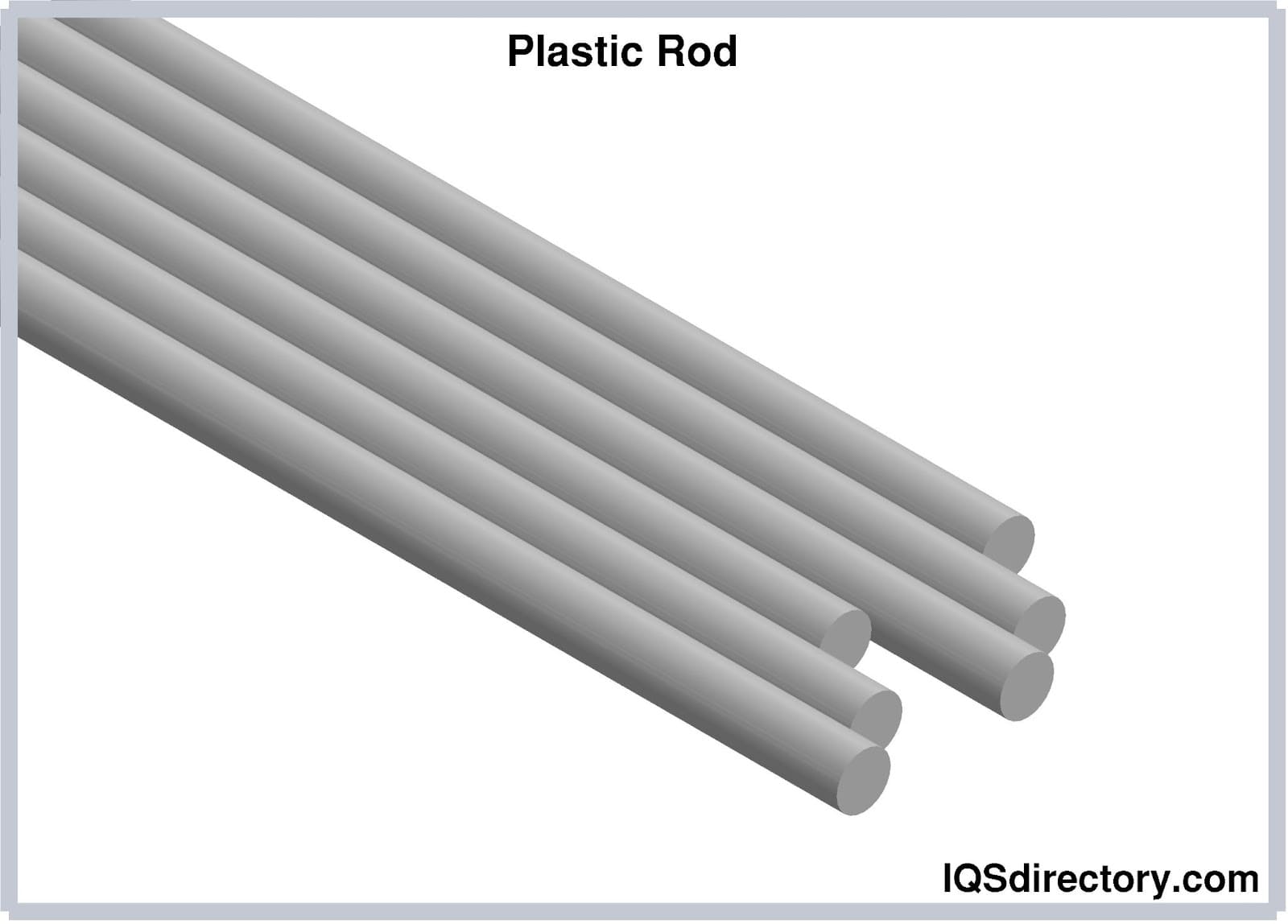
Superior Item Flexibility
Past the cost-effectiveness of plastic extrusion, an additional considerable benefit in making lies in its superior item adaptability. This makes plastic extrusion an excellent service for sectors that need personalized plastic components, such as auto, building and construction, and packaging. In essence, plastic extrusion's item flexibility fosters advancement while boosting functional effectiveness.
Enhanced Production Rate
A considerable advantage of plastic extrusion hinges on its boosted manufacturing rate. This manufacturing process enables high-volume production in a fairly brief time period. It is over here capable of producing long, constant plastic profiles, which significantly lowers the production time. This high-speed manufacturing is especially advantageous in industries where huge amounts of plastic parts are needed within tight due dates. Few various other manufacturing processes can match the speed of plastic extrusion. In addition, the capacity to maintain constant high-speed production without sacrificing item quality establishes plastic extrusion visit homepage aside from various other techniques. The improved production rate, for that reason, not only enables suppliers to fulfill high-demand orders but also adds to raised performance and cost-effectiveness. This advantageous attribute of plastic extrusion has actually made it a favored option in countless sectors.
Real-world Applications and Influences of Plastic Extrusion
In the realm of manufacturing, the strategy of plastic extrusion holds profound significance. This process is widely made use of in the manufacturing of a variety of items, such as plastic tubes, window structures, and weather condition removing. As an outcome, it considerably influences fields like building, product packaging, and vehicle industries. In addition, its effect encompasses daily items, from plastic bags to toothbrushes and non reusable cutlery. The financial advantage of plastic extrusion, primarily its cost-efficient and high-volume result, has reinvented manufacturing. The ecological influence of plastic waste remains a concern. Therefore, the market is constantly pursuing technologies in naturally degradable and recyclable products, showing a future where the advantages of plastic extrusion can be preserved without compromising environmental sustainability.
Conclusion
To conclude, plastic extrusion is a extremely effective and reliable method of changing raw materials into varied items. It uses many advantages over various other plastic developing approaches, consisting of cost-effectiveness, high outcome, minimal waste, and style flexibility. Its impact is greatly felt in various sectors such as building Visit Website and construction, auto, and customer items, making it a pivotal procedure in today's production landscape.
Diving deeper into the technological process of plastic extrusion, it starts with the option of the ideal plastic material. Once cooled down, the plastic is reduced into the called for sizes or wound onto reels if the item is a plastic movie or sheet - plastic extrusion. Comparing Plastic Extrusion to Various Other Plastic Forming Techniques
Comprehending the types of plastic suitable for extrusion leads the way for a more comprehensive conversation on exactly how plastic extrusion piles up against other plastic developing techniques. Few various other manufacturing processes can match the speed of plastic extrusion.
Report this page